Category

Contact
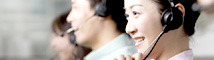
Tel: ( 86) 755-26996606
Fax: ( 86) 755-26007653
E-mail: rosemary@ussharp.com
Woods-tiger@ussharp.com
Web site: www.ussharp.com
Address: Floor 4, Jinhui Building, Nanhai Road, Nanshan District, ShenZhen

News
Physical-vapor-deposition (PVD) coatings also offer advantages over CVD coatings in certain operations and/or workpiece materials. Commercialized in the mid1980s, the PVD coating process involves relatively low deposition temperatures (approximately 500°C), and permits coating of sharp insert edges. (CVDcoated insert edges are usually honed before coating to minimize the effect of eta phase.) Sharp, strong insert edges are essential in operations such as milling, drilling, threading and cutoff, and for effective cutting of longchipping materials such as lowcarbon steels (Figure 4, at below). In fact, a wide range of “problem” materials—such as titanium, nickelbased alloys, and nonferrous materials—can be productively machined with PVD coated tools. From a workpiece structure point of view, sharp edges reduce cutting forces, so PVD coated tools can offer a true advantage when machining thinwalled components.
The first PVD coatings were titanium nitride (TiN), but more recently developed PVD technologies include titanium carbonitride (TiCN) and titanium aluminum nitride (TiAlN), which offer higher hardness, increased toughness, and improved wear resistance. TiAlN tools in particular, through their higher chemical stability, offer increased resistance to chemical wear and thereby increased capability for higher speeds.
Recent developments in PVD coatings include “soft” coatings such as molybdenum disulfide (MoS2) for dry drilling applications. Combination soft/hard coatings, such as MoS2 over a PVD TiN or TiAlN, also show great potential, as the hard (TiN or TiAlN) coating provides wear resistance while the softer, more lubricious outer layer expedites chip flow.
Related information
- 2012-12-23Efficiency of Milling Cutters
- 2012-11-11Turning Machines
- 2012-10-16Ceramics For Difficult Materials
- 2012-07-15New Irons In The Fire
- 2012-04-07Nonferrous Fulfillment
