Category

Contact
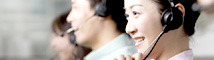
Tel: ( 86) 755-26996606
Fax: ( 86) 755-26007653
E-mail: rosemary@ussharp.com
Woods-tiger@ussharp.com
Web site: www.ussharp.com
Address: Floor 4, Jinhui Building, Nanhai Road, Nanshan District, ShenZhen

News
we highly recommend milling a typical mold cavity with a ball nose insert tool. This includes cavities with shallow or steep angle and straight (perpendicular) walls. The large radius of a ball nose tool will be able to cut faster than square or bull nose tools; the ball nose insert will create a smoother transition and leave a more even stock for semi-finishing. Square and bull nose tools typically leave “steps” resulting in very uneven stock, causing changing machining forces and increased tool deflection for semi-finishing. Rest milling of small details (small radii, sharp corners, etc.) can be done with other tools once the cavity has been finished with the ball nose tool.
Ball nose tools have other important advantages. They can be run at higher rotational speeds and feedrates than other tools when using milling strategies and parameters developed by Millstar. Whether milling aluminum, annealed steel, pre-hard or through-hardened die/mold steel, we recommend ball nose tools as first choice. The primary strategy we recommend is milling the cavity with a "Z-level" (X – Y contour) tool path. Start the first pass by straight or helical ramping (1-3° ramp angle) to the recommended depth of cut (ap). This allows the feedrate to remain the same as in the Z-level cut. We do not recommend plunging or peck drilling to depth. Preferably work from inside out to the periphery of the cavity in a climb milling (down milling) tool path. In the first pass the tool is engaged in a channel cut and the cutting edges are “in the cut” for 180 degrees. This imparts more heat into the tool, but the channel cut is relatively short. Working from the periphery toward the center, the peripheral first channel cut is far longer; the heat generated is higher and would require the tool to be run slower. The step-over or pitch (ae) for roughing and semi-finishing should follow Millstar recommendations. Typically the step-over in HS rough and semi-finish milling is 20 – 45 % of tool diameter. This keeps the cutting edge “in the cut” for a shorter time and gives the cutting edge less time to heat up. It also keeps the tool “on center” as it cuts on both sides of the tool’s axis and minimizes tool deflection.
We do not recommend drilling starting holes in corners or center of a cavity. They lead to interrupted cutting, possible chip re-cutting and additional cutter entries and exits during cutting, which lead to unnecessary thermal and load shocks on the cutting edge.
Related information
- 2012-12-23Efficiency of Milling Cutters
- 2012-11-11Turning Machines
- 2012-10-16Ceramics For Difficult Materials
- 2012-08-07PVD:Sharp for Steel
- 2012-07-15New Irons In The Fire
